New AE II discharge power system breaks through old machining limits, which means faster cycle time, better surface finish, and lower electrode wear.
Z axis fast jumping speed 18M/min
The new AE II type motion control algorithm improves debris removal speed. The spindle can reach high-speed movement of 18M/mm to remove debris, which is nearly 9 times faster than the original AI model. In large-area and precision machining discharge occasions, stable servo motion control is provided to improve discharge efficiency and shorten machining time.
Workpiece
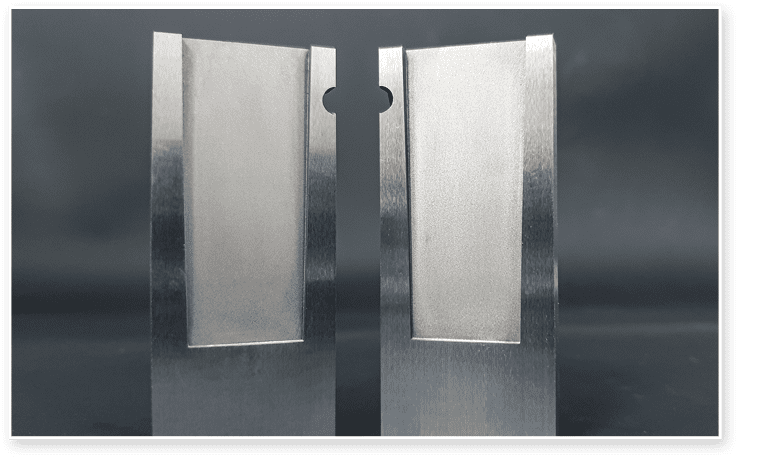
Item | Content |
Electrode | Graphite POCO EDM 2 |
Workpiece | SKD 11 |
Projection area | 1 x 38 mm |
Machining depth | 70 mm |
Surface roughness | VDI 25 / Ra 1.8 um |
Mirror surface Ra 0.08um
The ultra-fine surface Ra 0.08 um can be easily reached even in a large area without using powder technology, saving time for further polishing treatment.
Workpiece
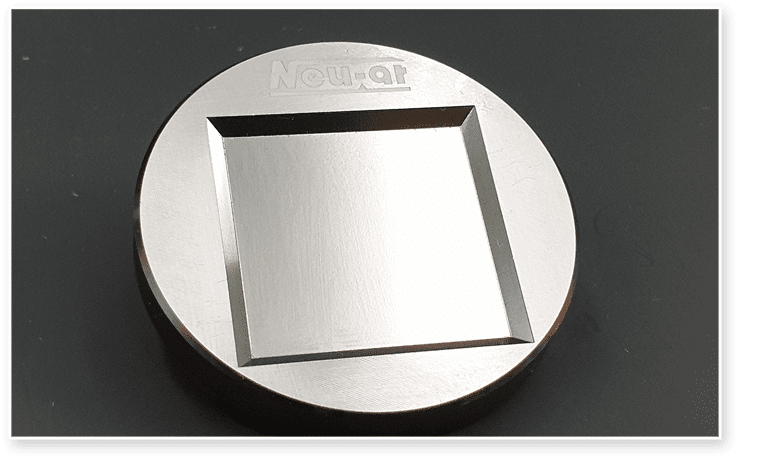
Item | Content |
Electrode | Copper |
Workpiece | NAK 80 |
Projection area | 35 x 35 mm |
Machining depth | 1.97 mm |
Machining time | 5 hours 15 minutes |
Surface roughness | VDI 0 / Ra 0.08 um |
Sharp corner R radius 8um
As electronic products move toward high-precision and miniaturization, the requirement standards for machining are getting higher and higher. For finer lines and shapes, through the latest wear suppression technology, the best R angle 8um can be achieved.
Workpiece
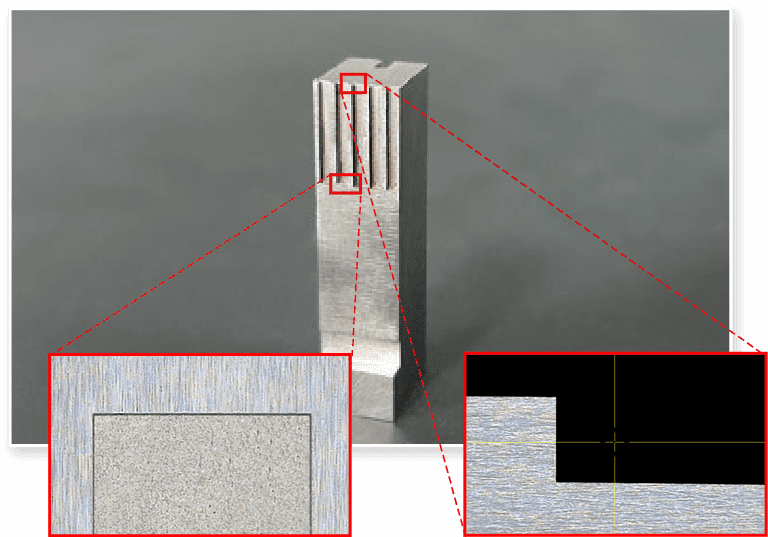
Item | Content |
Electrode | Copper |
Workpiece | VIKING |
Undersized calculation | 0.05 mm |
Number of electrodes | 4 |
Machining depth | 0.3 mm |
Surface roughness | VDI 7 / Ra 0.22 um |
Super harden material machining
The high tool wear caused by super hard materials is a major problem in electrical discharge machining. Through a new exclusive super hard alloy circuit and low wear technology , the sharp corner R radius can be clearly displayed. The best surface roughness can reach up to Ra 0.22 um.
Workpiece
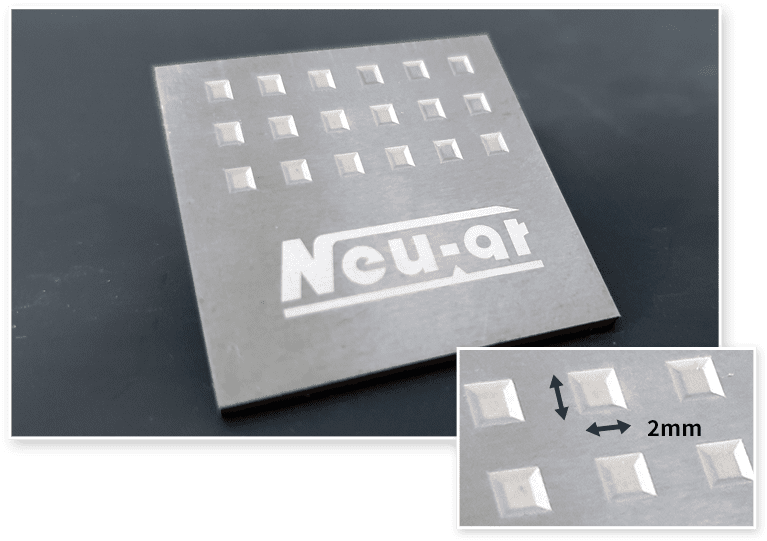
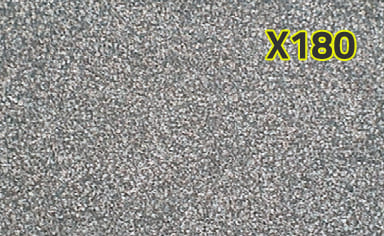
Previous technology
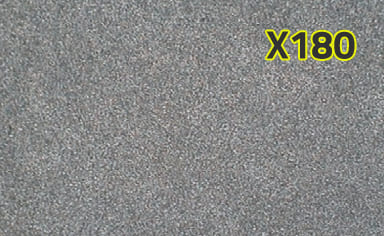
AE II New technology
Item | Content |
Electrode | Copper Tungsten |
Workpiece | Tungsten-Carbide HRA 90° |
Projection area | 83 mm2 |
Machining depth | 0.15 mm |
Machining time | 2 hours 10 minutes |
Surface roughness | VDI 7 / Ra 0.22 um |
Fine finishing machining
Newly developed discharge power circuit, significantly fine finishing machining performance improved , compared with the previous generation, cycle time reduced by nearly 45%.
Workpiece
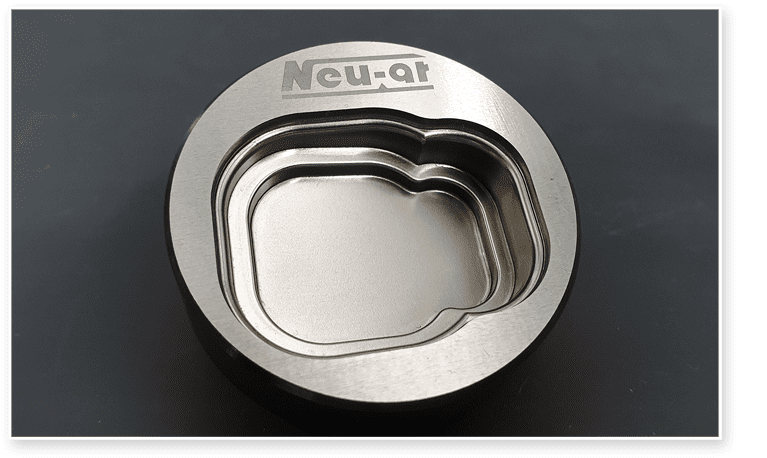
Item | Content |
Electrode | Copper |
Workpiece | NAK 80 |
Projection area | 38 x 28 mm |
Machining depth | 12 mm |
Machining time | 6 hours 9 minutes |
Surface roughness | VDI 9 / Ra 0.28 um |
Large area machining technology
The larger the workpiece area and the finer the surface, the more uneven particles will appear. The new AE II power supply, through monitoring high-speed discharge gap state , can result an even machining surface, improving the efficiency, and greatly reduce the subsequent mold polishing time.
Workpiece
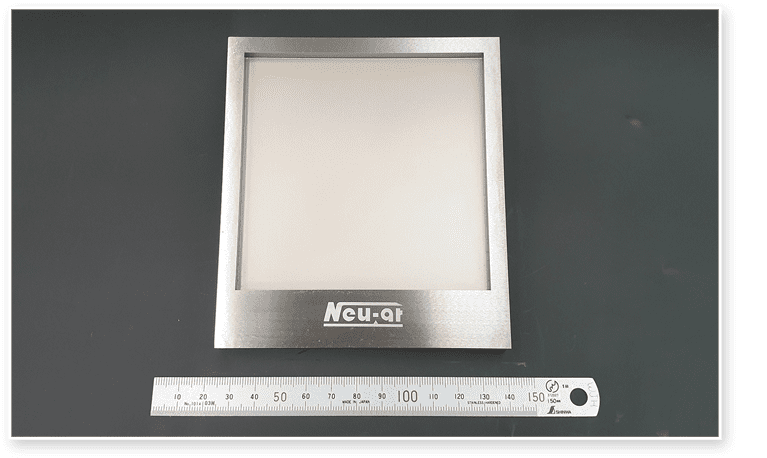
Item | Content |
Electrode | Graphite POCO EDM 200 |
Workpiece | SKD 61 |
Projection area | 100 x 100 mm |
Machining depth | 5 mm |
Machining time | 6 hours 21 minutes |
Surface roughness | VDI 18 / Ra 0.8 um |